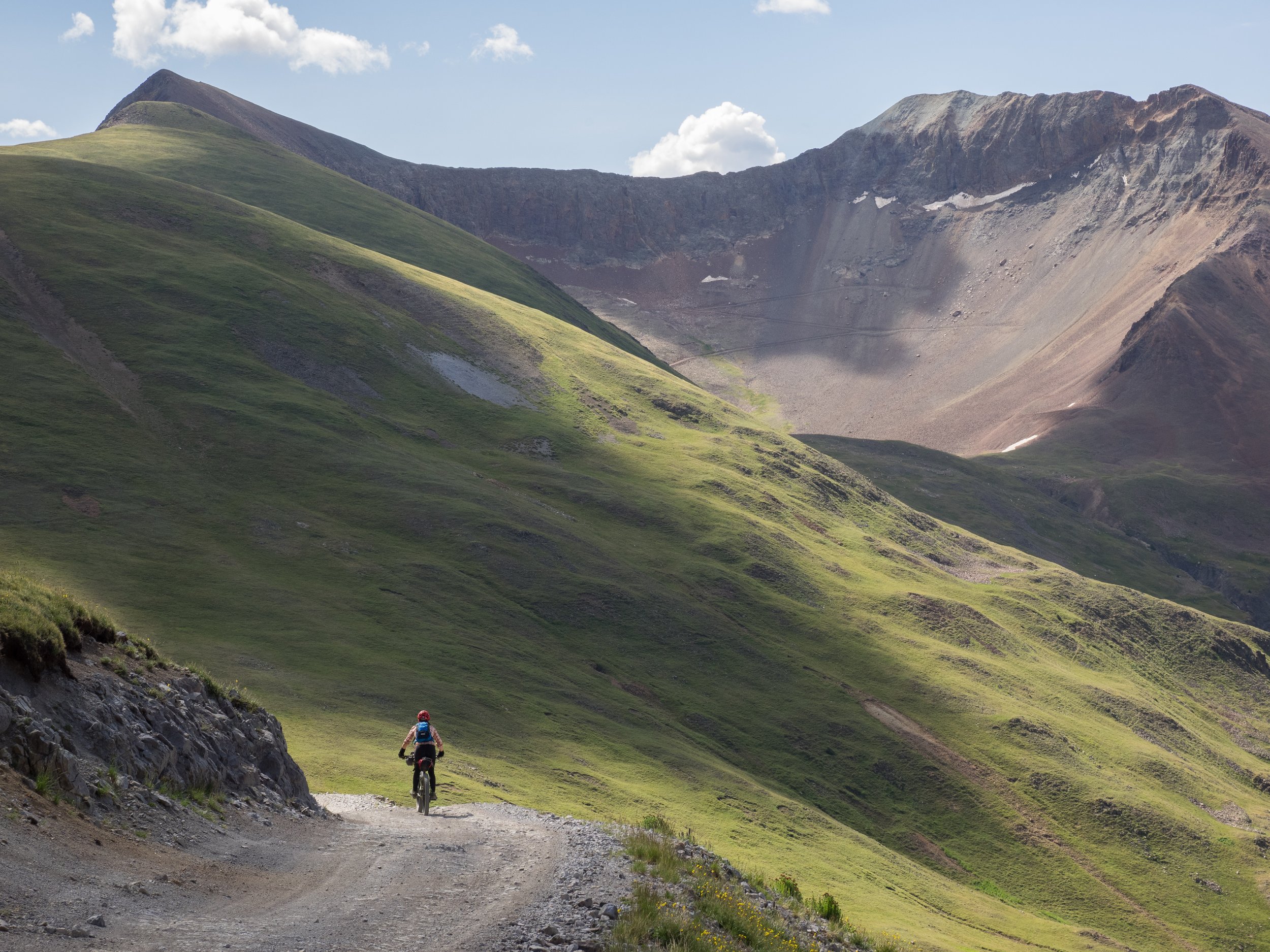
PROCESS & MATERIALS
What sets Bedrock apart? Unlike in 2012, when we established Bedrock, there are now many bikepacking gear manufacturers out there. Some of our competitors do great work. Some outsource poor designs to overseas factories with poor build quality. Some have even blatantly copied our innovations!
Regardless of how many companies are now in the market, we stand by our business principles: Quality, Originality, Design, and Customer Service. While these may seem cliche, we honestly strive to uphold these in everything we do.
Quality: We use the best materials for each specific purpose, and we pay attention to the details. We are committed to keeping production in the USA and directly under our roof.
Originality: Virtually every piece of gear we produce has some critical function or feature that sets it apart from other options.
Design: Both functional and aesthetic. 1) Functionally, we design bags that are rock-solid in real world conditions. 2) Aesthetically, Bedrock gear has a consistent aesthetic. Tailored. Tight. Clean.
Customer Service: The best gear out there doesn't matter if customer service is terrible. So we make service a priority. This means we are responsive, proactive, and keep our promises.
ABOUT OUR MATERIALS
We use the highest-quality materials we can find, and choose US-made whenever possible. Most of the fabrics you see in our products are made on American soil by Dimension Polyant and are part of their well-known X-Pac line. We use everything from X-Pac VX21-RS to X50, though we also use many other materials in various parts of our bags - 1680 ballistic nylon, various synthetic rubber textiles, various packcloths, and much more.
We choose each material for the demands of the role it must fulfill - which is why many of our bags have several different fabrics in each piece.
Depending on what color you choose when ordering, your gear will feature slightly different fabric. All our fabrics have passed our stringent performance standards. But - to split hairs - if you want the most bomber fabric we use, select the Dark Camo color. If you want the lightest, plain old black is your color (although we’re talking a few grams, not ounces). We suggest simply ordering whatever color you think looks best, because the performance and weight differences are imperceptible.
WHY NOT 100% “WATERPROOF”?
“On this particular day in early September it rained for around 6 hours straight and my sleep system and mobile phone inside them were bone dry!” -Steve B., Scotland
Virtually every material and closure we use is waterproof. However, our gear is sewn, because stitching textiles is the strongest way to build a bag. Under heavy rain events (or submersion), you may see some dampness enter your bags through the seams. With the advent of welded-PVC bikepacking gear several years ago, “why not waterproof?” is a question we’ve heard a time or two. Happily, there are great reasons to worry less about “waterproof” and more about real-world performance:
1) "Waterproof" doesn't mean no water enters your bags. Camping gear gets wet, and then goes into your bags - condensation-soaked shelters, sweaty clothing, rain gear after the storm has passed. In reality, regardless of what type of bags you use, you must always individually waterproof critical items. Instead of imagining the inside of your bags will stay 100% dry, the best real-world approach is to use highly weather-resistant bags and use simple plastic bags to keep your critical items protected.
2) Lower-quality materials and assembly. Making a 100% waterproof bag means RF-welded construction on material that is less abrasion-resistant. RF-welding doesn’t work with the durable materials we choose to use for our gear. Additionally, welded seams aren’t as durable as sewn seams - no bag is waterproof once the seams bust open! Case in point: A leading American moto gear manufacturer makes both sewn and welded bags. Warranty on the sewn bags is 10 years; warranty on the welded is only 1 year. This is why we sew our gear.
3) Lower-quality product and outsourced jobs. The technology to RF-weld largely belongs to overseas manufacturers at this point, and the bags we see from those factories are poorly made. We are committed to detailed, skilled domestic manufacturing.
— — —
Our gear has been used around the world in every weather condition imaginable and on innumerable packrafting trips. Judging from our own long experience as well as that of our customers, the quality materials and construction techniques we use far outweigh any benefits of welded bags.
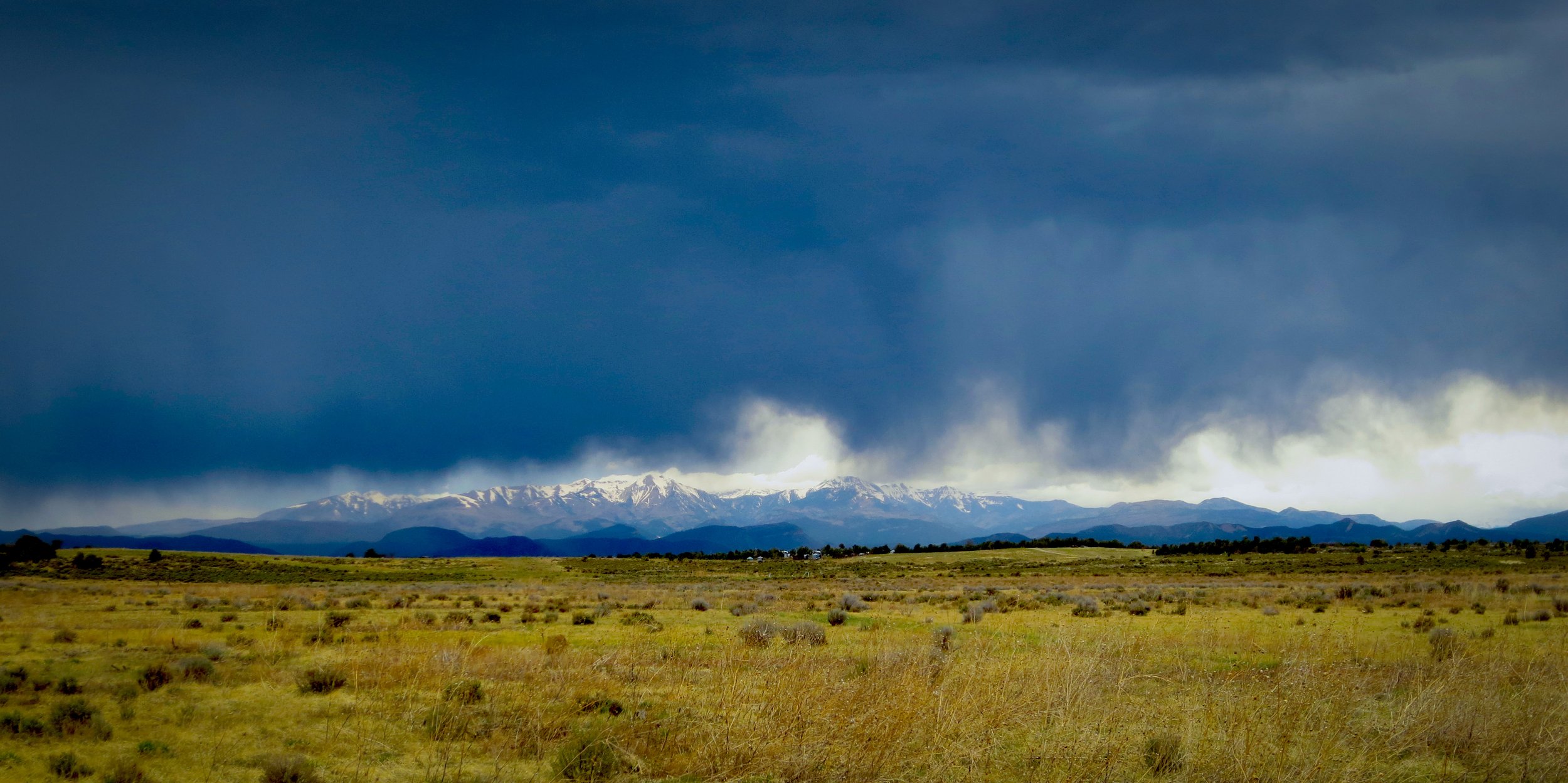